В предыдущем номере мы рассказывали о «заповедях» автосамодельщика, а сегодня в нашей школе начинающего автоконструктора — первый урок, посвященный расчету рамы — основного несущего элемента машины. Мы не ставили цели строго следовать очередности «заповедей», чтобы при необходимости иметь возможность вновь возвращаться к отдельным темам. В перспективе — статьи о компоновке, дизайне и, конечно же, расчеты — в объеме, необходимом для проектирования и представления в ГАИ при регистрации автомобиля.
Надо ли говорить, что всякий автомобиль является источником повышенной опасности? Пожалуй это и так ясно каждому. Любая поломка, случившаяся на трассе, грозит серьезным происшествием, опасным и для водителя, и для пассажиров, и для прохожих. Поэтому при регистрации самодельного транспортного средства необходимо предъявить расчеты на прочность его рамы и основных узлов, от которых зависит безопасность.
Подобный расчет может быть выполнен по предлагаемой мною методике. Она сравнительно проста, не требует специальной инженерной подготовки и вместе с тем обеспечивает определение параметров металлоконструкции с достаточной точностью. Последовательность расчета следующая: найти центр тяжести машины, определить действующие на раму усилия, составить схемы действующих сил, построить эпюры изгибающих моментов, выявить опасное сечение, определить напряжения изгиба и запас прочности. Приведенная здесь методика дается на примере микроавтомобиля «Минимакс» конструкции автора (см. «М-К» № 1 за 1975 г. и № 11 за 1982 г.), однако она может быть с успехом применена и для самодельных автомобилей других систем.
Нахождение центра тяжести
Центр тяжести (ЦТ) машины определяется графически. Для этого на бумаге в клетку или миллиметровке в избранном масштабе вычерчивается схема автомобиля, на которой прорисовывается компоновка и наносятся точки, соответствующие центрам тяжести всех основных узлов (рис. 1).
Если отдельные элементы размещены несимметрично относительно продольной оси, необходимо выполнить в том же масштабе вторую проекцию.
Далее заполняется таблица: последовательно в каждой графе указываются соответствующие точкам узлы, их вес (масса) и координата X — расстояние до нулевой отметки по оси машины. Вес кузова и рамы распределяется по длине достаточно равномерно; в данном примере смещение их ЦТ вперед учитывает некоторое утяжеление передней части, вызванное особенностями вагонной компоновки «Минимакса».
Координата ЦТ машины определяется из общей суммы произведений веса каждого узла на собственную координату, деленной на полный вес автомобиля. Для нашего случая:
XЦТ=(ΣGiXi)/(ΣGi)=164900/1000=165(см)
где: Gi — вес отдельного узла,
Xi — координата отдельного узла,
ХЦТ — координата ЦТ машины.
Из схемы и соответствующей ей таблицы нетрудно определить распределение нагрузки по осям, исходя из условия, что сумма моментов сил относительно любой из осей должна быть равна нулю. Так, относительно задней оси:
ΣGi*(Х02— ХЦТ ) = G01 * (Х02-Х01),
где: Х02 — координата задней оси, Х01 — координата передней оси, G01 — нагрузка на переднюю ось.
Тогда:
G01=ΣGi*(X02-XЦТ)/(X02-XЦТ)=1000(240-165)/(240-80)=~470(кгс)
Соответственно, нагрузка на заднюю ось составит: G02 = ΣGi-G01= 1000-470 = 530 (кгс).
Расчет усилий, действующих на раму
Вес некоторых перечисленных в таблице компонентов не воздействует на раму. Так, под нею находятся подвески с колесами. Можно пренебречь и массой кузова, поскольку она сильно распределена по длине. Дело в том, что кузов имеет довольно жесткую конструкцию, надежно соединенную с лонжеронами, что не увеличивает, а, наоборот, уменьшает нагрузки на раму (соответственно повышая и запас прочности).
При прочностном расчете автомобиля применяется так называемый динамический коэффициент, учитывающий перегрузки, возникающие в момент наезда на неровности дороги. Обычно такой коэффициент принимают равным 1,75, хотя у автомобилей повышенной проходимости он может быть и выше. Величина динамической нагрузки Р = 1,75 G указана в последнем столбце таблицы. Суммарное значение расчетной нагрузки равно 989 кгс, а координата ЦТ составит:
ALIGN=»JUSTIFY»>Х1ЦТ=Σ*Xi/ΣGi=97625/560=174 (см)
ТАБЛИЦА ДЛЯ РАСЧЕТА НАГРУЗКИ
На автомобиль в целом | На раму | |||||
Узлы | Вес G, кгс | X, см | G*X | G | G*X | р= 1,75*G, кгс |
Запасное колесо | 5 | 0 | 0 | 5 | 0 | 9 |
Рулевое управление | 10 | 35 | 350 | 10 | 350 | 18 |
Система управления, приборы, сиденья | 40 | 40 | 1600 | 40 | 1600 | 70 |
Передняя подвеска | 45 | 75 | 3375 | — | — | — |
Водитель и передний пассажир | 150 | S5 | 14250 | 150 | 14250 | 262 |
Рама | 50 | 150 | 7500 | — | — | — |
Кузов | 250 | 150 | 37500 | — | — | — |
Колеса в сборе | 40 | 160 | 6400 | — | — | — |
Пассажиры (заднее сиденье) | 150 | 185 | 27750 | 150 | 27750 | 262 |
Бензобак | 5 | 185 | 825 | 5 | 925 | 9 |
Бензин | 40 | 185 | 7400 | 40 | 7400 | 70 |
Задняя no-веска | 50 | 230 | 11500 | — | — | — |
Силовой агрегат | 125 | 270 | 33750 | 125 | 33750 | 219 |
Аккумулятор и электрооборудование | 40 | 290 | 11600 | 40 | 11600 | 70 |
В сумме | ΣGi =1000 кгс | ΣGiXi=164900 кгс*см | Σ1Gi =560 кгс | Σ’GiXi=97625 кгс см | ΣР =989 кгс |
Нагрузка на переднюю ось определяется аналогично расчету, приведенному по формуле 2. R01=ΣP*(X02-X1ЦТ)/(X02-X01)=989(240-174)/(240-80)=408(кгс) Соответственно, на заднюю ось приходится нагрузка: R02=ΣP-R01 = 989-408=581 (кгс). Обе нагрузки R01 и R02 передаются на четыре попарно расположенные поперечные трубы рамы через подвески. Таким образом, схему действующих сил можно представить в виде рисунка 2А, где на четыре шарнира рамы действуют реактивные силы, равные половинам R02 и R01. Над основной рамой параллельно ей установлены дополнительные элементы, передающие нагрузку от силового агрегата, пассажиров и бака с топливом на те же самые поперечные трубы. Разложив каждый из этих весов на составляющие (пропорционально плечам), получим, что противоположно направленные силы взаимно исключат друг друга. Следовательно, расчетная схема примет вид, показанный на рисунке 2Б. Эпюра изгибающих моментов строится по оси ординат как сумма произведений силы на соответствующее плечо. Так, для сечения А изгибающий момент в кгс*см составит: МА = 9*50+18*15 + 70*10= 1420 (кгс*см). Аналогично для сечения Б: МБ =9*110+18*75+70*70-138,5*60 = -1070 (кгс=см). Выбор опасного сечения Опасными называют сечения, где возникают максимальные напряжения. Обычно таковыми являются места наибольшего изгибающего момента и наименьшего момента сопротивления профиля металлоконструкции. В нашем случае сечение лонжеронов рамы одинаковое — прямоугольная стальная труба 50X25 мм с толщиной стенки 2,5 мм. Поэтому опасным будет сечение А, соответствующее максимальному моменту МА = 1420 кгс*см. Расчет момента сопротивления Момент сопротивления W обычно определяют по справочникам для определенного сортамента профиля. Однако его нетрудно и рассчитать. При использовании прямоугольной трубы: W=(BH3=bh3)/(6H) где W — момент сопротивления, В, b, H, h — соответственно наружные и внутренние ширина и высота трубы (рис. 3). В нашем случае: W =( 2,5*53-2*4,53)/(6*5)=~ 5,5 см3. Для круглой трубы момент сопротивления можно определить по формуле: W = 0,1(D3— d3), где: D и d — соответственно наружный и внутренний диаметры. Расчетные напряжения и запас прочности Поскольку изгиб рамы воспринимается двумя продольными лонжеронами, то на каждый из них придется лишь половина момента. Таким образом, напряжение изгиба будет равно: σИЗГ=MMAX/(2W)=1420/(2*5.5)=116 кгс/см2 Для обычной углеродистой стали без термообработки допускаемое напряжение составляет: [σизг]<=1500 кгс/см2. Соответственно запас прочности: n=[σизг]/σизг=1500/116=11.6 В целом запас прочности должен быть не менее n = 2. Полученное в нашем примере столь большое значение не случайно. Это результат удачно выбранной схемы, в которой изгибающие моменты «гасят» друг друга. Так, если бы над рамой не было дополнительных продольных элементов, то нагрузки от веса двигателя и пассажиров вызвали бы моменты в продольных лонжеронах в 3-4 раза выше, чем сейчас. Такой прием локализации силовых нагрузок можно рекомендовать всем любителям автоконструирования. Масса рамы «Минимакса», включая четыре поперечины и дополнительные трубы, составляет всего 45 кг, или примерно 7% от конструктивной массы машины. В принципе, исходя из большого запаса прочности, возможно и дальнейшее снижение веса, однако при этом не следует забывать о жесткости металлоконструкции. П. ЗАК |
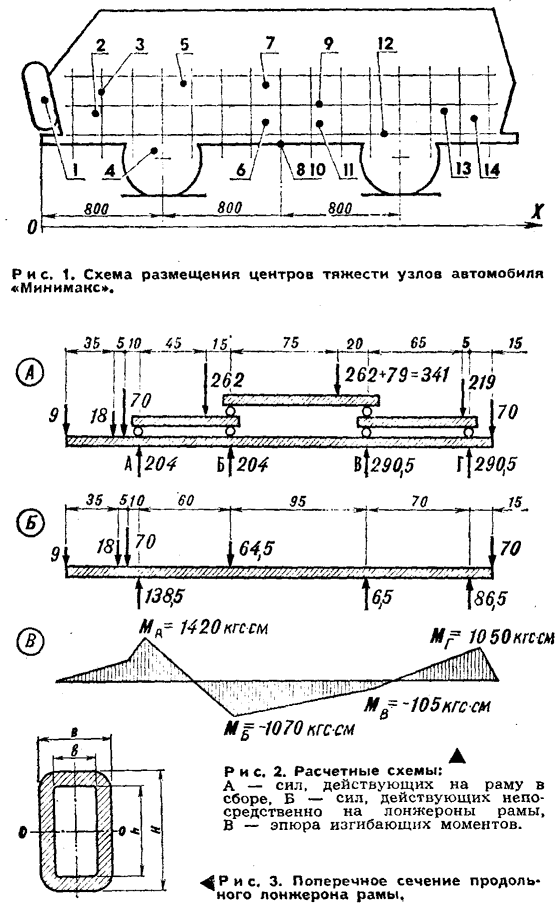
Источник: «Моделист-Конструктор» 1988, №7 |